Integration of fluid power engineering
Dörries Scharmann Technologie GmbH (DST) used the migration to the new EPLAN platform to also integrate fluid power engineering.
Dörries Scharmann Technologie GmbH (DST) used the migration to the new EPLAN platform to also integrate fluid power engineering. Now, electrical designers work even closer together with their colleagues in hydraulic and pneumatic design - both disciplines use the same platform. This offers many advantages, and at the ECAD level, everyone benefits from the more direct communication with enclosure service providers. An aircraft manufacturer wants to have a 5-axis machining center to machine complex aircraft structure components; a manufacturer of wind turbines wants to more accurately and flexibly machine three tons of turbine parts. These are two typical orders for engineers at Dörries Scharmann Technologie GmbH (DST), located in Mönchengladbach. DST, with its Dörries, Droop + Rein, Scharmann, Berthiez and Mecof brands, has focused on the development and production of machine tools that fulfill special precision and speed requirements. When it comes to size, some of the DST machines are world class: In Mönchengladbach, large machining centers for 25 meter long pieces have been produced. A recent example: One of the company's current orders is for a system with seven high-performance ECOSPEED F machining centers for the Korean aircraft manufacturer, KAI Korea Aerospace Industries Ltd. The milling machining centers are for machining Airbus A 350 XWB wing structural elements known as wing ribs. According to DST, the most productive solution for high-performance cutting of aluminum structural components is used: the parallel kinematic Sprint Z3 machining head, which is standard equipment in all ECOSPEED machines. The high performance of these machines is clearly reflected in the performance of the main spindle: it is equipped with drives up to 120 kW and works with rotation speeds up to 30,000 min-1. Smooth migration from EPLAN 5 to the new platform
Electrical design at DST carefully planned the migration from EPLAN 5.70 to EPLAN Electric P8 and extensively looked into which additional new functions made sense. Dipl.-Ing Christian Nientimp, head of electrical hardware at DST and responsible for the implementation of the new platform: "Because we definitely wanted to maintain the productivity of our department, we decided to start with the basic functions and introduce more functions one step at a time. A major reason the migration was accomplished without hurting productivity was the extensive experience of the electrical designers; they drove the migration and had in-depth knowledge of earlier EPLAN versions." The strategy paid off: "The migration from EPLAN 5.70 to P8 went very well. We also benefited from the simultaneous introduction of a new control generation. Integrating fluid power engineering
DST also uses a new CAE system in fluid power engineering – on a data basis consistent with electrical engineering. The EPLAN platform makes it possible for electrical engineering and fluid power engineering to work at a single design level, which has practical benefits. Christian Nientimp: "Previously, fluid power design, which is part of mechanical design at DST, worked with another CAD tool. In the case of these very complex electrohydraulic and electropneumatic design parts, the result was that the data basis of the two design departments was not consistent. Automatic data synchronization was therefore not possible. Despite excellent and intensive department cooperation, inconsistencies could not be avoided, causing extra work. Time loss was unavoidable." "The plans contain significantly more information"
In addition to the time savings, DST was pleased with the substantially more accurate design data: Many dimension parameterizations are now stored in the system and are therefore available to both the electrical and the fluid power designers. Both disciplines can also be sure that they always use the same version of the drawing since they work on a consistent data basis. All of this affects everyday design work. Christian Nientimp: "The plans contain significantly more information." And if an error should occur, it is usually found by the EPLAN platform diagnostics function. Simple connection between electrical engineering and fluid power engineering
Fluid power engineering plays a significant role in design at DST. Many machines are equipped with hydrostatic bearings or hydraulic chucks. Compressed air is needed to blow off chips, to operate pneumatic axes (e.g. in tool changers), and as sealing air in measuring systems. Since almost all functions are electrically controlled, it makes sense to integrate electrical engineering and fluid power engineering. Since EPLAN Fluid was introduced, the two fluid power designers work even more closely together with the eight electrical designers. The references between the two disciplines are always visible in the drawings: The hydraulic and pneumatic standard designations as well as the electrical identifiers are stored in the schematics, making cross-references immediately visible in both directions. More data – put to better use
Electrical engineers basically create two types of diagrams: function diagrams that show the PLC inputs and outputs, for example, and location-specific installation diagrams with the electrical connection diagrams that are used as working diagrams for the workshop. The complete electrical schematic for a machine, including the interconnect diagrams has around 700 to 800 pages. Of these pages, 80 to 100 are related to fluid power. Even the data basis used by the designers is more detailed, because EPLAN Electric P8 allows lists for design data to be freely parameterized. DST uses this feature for pricing data and ordering data as well as for product-specific data such as dimension, weight, distances, heat dissipation and current consumption. This helps designers when choosing a product. Direct connection to enclosure production
A prerequisite is naturally that the parts database always be kept up to date. This task is taken very seriously at DST: Data for new products is entered immediately. This provides a sound basis for automatic generation of bills of material, which can be transferred directly to the external enclosure producer, Siemens WKC in Chemnitz. Since Siemens also uses the EPLAN platform and the third system, EPLAN Cabinet, cooperation during enclosure planning and production is significantly easier. Christian Nientimp: "Previously, we used add-on applications prepared by EPLAN for device and price lists. Now we can instantly create the parts lists from the ECAD system and transfer them to enclosure production. We have a continuous flow of information and because the Siemens component prices are stored in our system, we know what the enclosure costs as soon as the design has been completed. The enables us to quickly and accurately cost projects." It was also favorably noted that it was easier to connect projects and partial projects on the new platform. The structure diagram could also be more precisely planned since the installation spaces and free spaces are stored in EPLAN Electric P8. Consistent modularization
In view of the high engineering component and the fact that DST machines are usually developed or adapted to meet specific customer requirements, design modularization is very important. Christian Nientimp: "We are currently preparing the macro structure we will use in the future and are very carefully planning the optimum module size while striving to have a common basis for all product areas and machine sizes." Company-wide utilization with the viewing function
At DST, the EPLAN platform is not only used in design. Christian Nientimp: "Throughout the company, we have around 100 workplaces that are equipped with a viewing function which is used intensively – in sales and software development as well as in assembly and commissioning. The system is also used for orders. The company benefits from the large quantity of product-specific information that is stored in P8: "Colleagues save time because they don't have to search through data sheets. And since our macro library has also grown, this time saving effect will increase in the future." Everyone feels well prepared for future requirements since CAD technology has been brought up-to-date and engineers across all disciplines cooperate more closely.
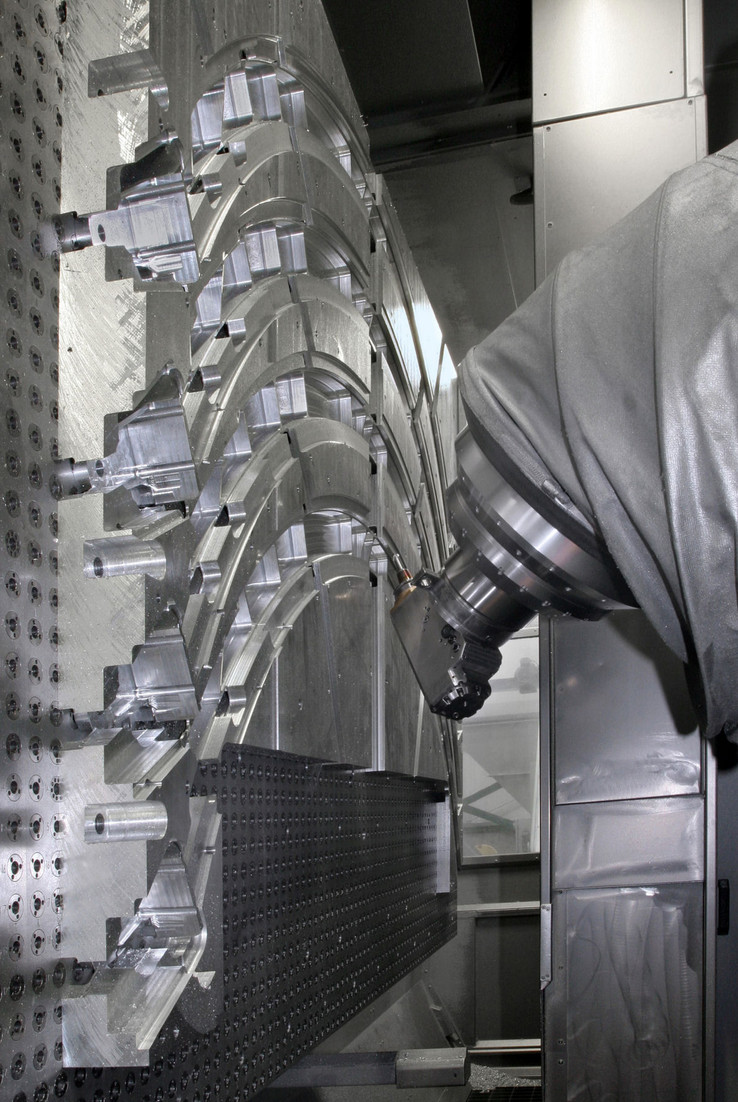
Typical milling process with the ECOSPEED F – a DST machining center for high- performance cutting of aluminum structural components.
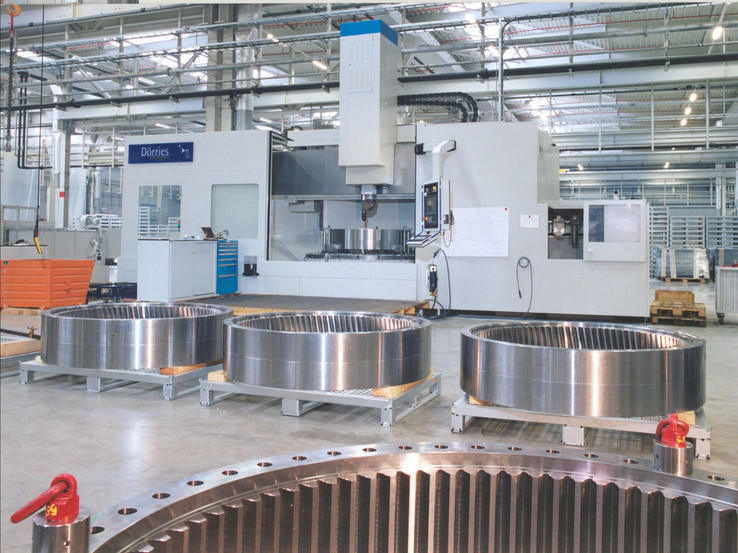
The vertical lathes from DST fulfill the highest precision and speed requirements and are used, for example, to build wind turbines.
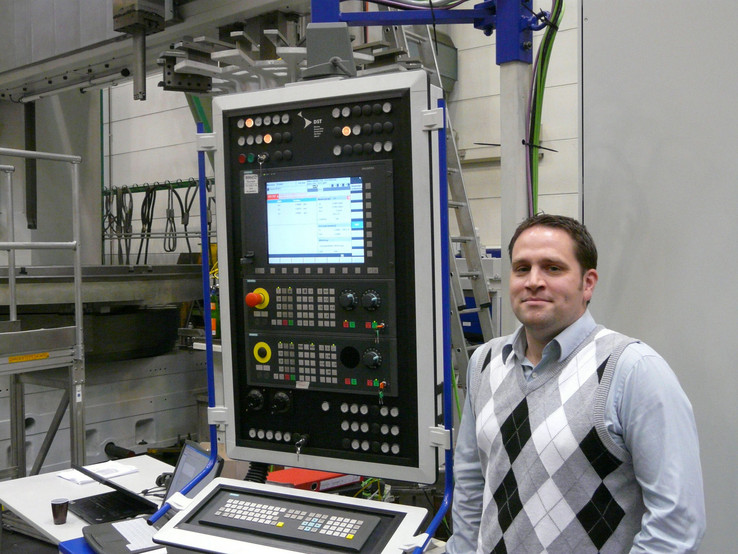
Even the control system reflects the size of the DST machines. Dipl.-Ing. Christian Nientimp: "We save time by integrating electrical engineering and fluid power engineering at the CAD level."